Machine room upgrade: complete
SafeLine invests in new machinery to meet the all-time high demand for SafeLine products caused by the digital switchover – increasing production speed and capacity and further strengthening the SafeLine quality.With the digital switchover happening all over Europe, the demand for future-proof SafeLine technology has skyrocketed over the last year.
The digital switchover, with technology moving away from analogue and 2G/3G solutions, has put pressure on customers to perform upgrades that comply with the new demands – but also on the industry to transform their product ranges.
"SafeLine now has a total of five pick-and-place machines – making up two complete production lines and increasing our production speed of up to 35% on some sections."
In response, SafeLine has taken several actions to be able to meet the demands of the market. The most prominent being an investment in new machinery for the SafeLine machine park – a.k.a. the SafeLine machine room, where all journeys towards the future of lift safety begins. SafeLine’s investment in a new pick-and-place machine will help make some sections of the surface mount production up to 35% faster.
– Our machine park is currently running at full speed here in Tyresö to be able to meet the exceptionally high demand from the market right now. SafeLine now has a total of five pick-and-place machines – making up two complete production lines and increasing our production speed of up to 35% on some sections. As soon as the global component shortages ease, we’ll be ready to supply the markets with products for years to come and quickly work ourselves back to normal delivery times, says Mattias Rosenström, head of the circuit board production at SafeLine’s production plant in Sweden.
Following the global unstable economic situation due to the pandemic, the increased demand for future-proof technology has led to drawn-out issues with component deliveries.
But thanks to SafeLine’s in-house development department, making changes to existing products can be done on-the-go – demonstrating the real benefits of having SafeLine’s technical resources gathered under one roof in Tyresö, Sweden.
– All of our departments are working as hard as they can to modify and adapt our current products to new components and materials to be able to deliver faster whenever necessary. It is due to the amazing work of our staff that we can maintain the high quality SafeLine is known for, ensuring product deliveries, says Geert Maurissen, SafeLine Group Managing Director.
"For us, it really has been a winning strategy. A benefit that comes with choosing SafeLine I don’t think a lot of customers are aware of."
Having all departments gathered under one roof was something that proved to be invaluable to SafeLine especially during the covid-19 pandemic, Geert Maurissen elaborates.
– Whenever a problem or question arises, what could otherwise have been drawn out over the course of one week can instead be solved during a single afternoon. For us, it really has been a winning strategy. A benefit that comes with choosing SafeLine I don’t think a lot of customers are aware of.
Uutiset
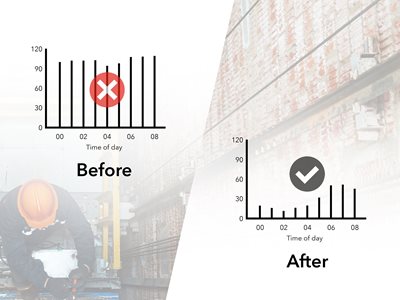
SafeLine LYRA -löytö leikkasi hissin huoltokustannuksia 20 %.
Hissi jätettiin pysyvään esittelytilaan asennuksesta lähtien, ja SafeLine LYRA -järjestelmän ansiosta hissin uskotaan pidentäneen hissin käyttöikää vuosilla ja vähentäneen huoltokustannuksia huomattavasti. "Jos LYRA olisi ollut asennettuna hissiin jo virheen tapahtuessa, virhe olisi havaittu välittömästi."

Anna hissien tulla luoksesi – SafeLine lanseeraa ORIONin ja LYRAn 🚀
Lanseerataan nyt: Digitaalisen SafeLine-etävalvonta-alustan ja innovatiivisen laitteiston ansiosta digitaaliset modernisoinnit ovat helposti käytettävissä kaikissa hisseissä ilman olemassa olevan asennuksen muuttamista.

SafeLine NOVA – uusi kosketuspohjainen kokemus
Lanseerataan nyt: SafeLinen CANopen-Lift-kosketusohjaimen uusi sukupolvi